Armstrong 104 Repad
Armstrong 104 Repad
21:03 on Saturday, February 27, 2010
|
|
 |
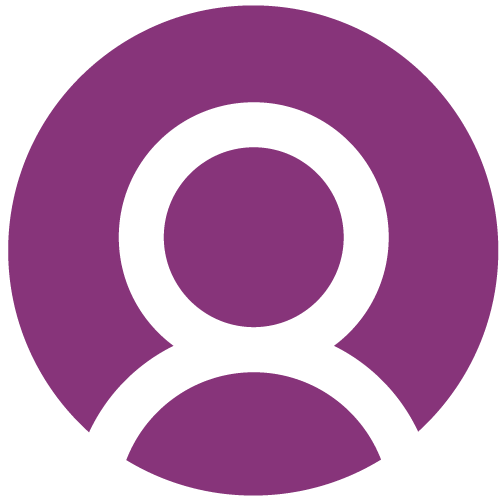 jim22 (247 points)
|
I got started today working on my old Armstrong flute. The flute is a 1970 vintage model 104. I have a couple of them and they are quite different. This one is the older of the two. The pads are held in with screws and metal washers. The newer one uses plastic snaps. Also the older one uses fewer different sizes of pads than the newer one. I should add that the one I'm working on was actually repadded professionally about 3 years ago, so the corks and felts are relatively fresh. The pads were ok, and it plays well enough, but some of the pads had apparently swollen a little and gotten leaky on the front edges.
I started with the headjoint cork. The old one was pretty loose and looked quite grungy. The plate that faces the tonehole is not exactly flat, and if it was ever plated the plating is gone. There wasn't much I could do with that. Also, there is some plating missing inside the tonehole itself. I think these issues contribute to a rather dull tone that I get from this flute. Anyway, I needed to trim the new cork to length. I glued the cork to the metal piece with hot glue. I sanded the leading end a tiny bit, put on some silicon grease, and pressed it in. The new one fits much better.
The next thing I did was disassemble, keeping all the parts sorted so that they went back on where they came from, and check the tone hole leveling. I used a glass microscope slide and a feeler to figure out where the gaps were and mapped them out for reference during shimming. A few tone holes were pretty good, but most had high spots either front and back or side to side of about .001". A couple had outages of about .002". I don't know much about fixing this, but these are rolled tone holes and removing material doesn't make much sense to me. At a minimum, I've got it mapped out. At one point I got a new pad in and shimmed level and the tone hole errors were clearly apparent. I should be able to put in a couple partial shims to get the pad to cover.
I ordered a variety of pads from Music Medic. I was able to decide on pad diameters that I will need to finish the job. Pad thicknesses is a little more mysterious. The pads in it are marked "premium deluxe" on the back and had no shims anywhere except where I had put them to get the swollen pads to seal. I ordered some in 2.7mm, and some in 2.9mm. I also ordered some .001" and .004" shims. It appears that the typical stack using a 2.7mm pad is between 4 and 6 of the .004" shims, which seems like a lot. If I put in a 2.9mm, you'd think that I could remove 2 shims, but in practice, the same stack might require only 1 shim, so the pads must not be exact thicknesses. I'm definitely starting to see the advantage of stocking a variety of sizes so that I can pick the most appropriate size for each key.
No other big surprises. I did find one loose spring. It didn't want to pull all the way through, but I should be able to peen the end a little so it holds in position. In general, some springs seen too strong, others too weak. I'll have to tweak them to make the action feel more consistent from key to key.
Jim
|
|
 |
|
Re: Armstrong 104 Repad
14:22 on Monday, March 1, 2010
|
|
|
Re: Armstrong 104 Repad
18:25 on Monday, March 1, 2010
|
|
|
Re: Armstrong 104 Repad
22:37 on Friday, March 5, 2010
|
|
 |
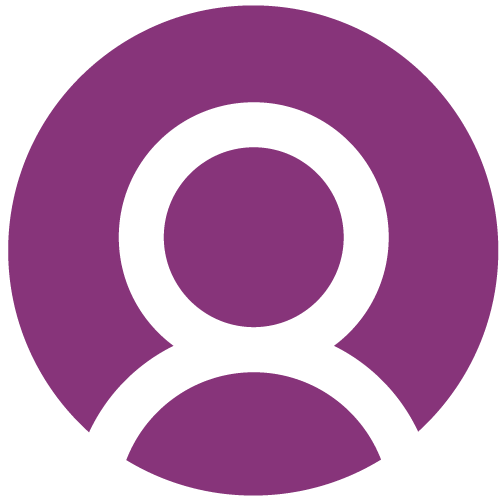 jim22 (247 points)
|
Reflections on the first attempt....
I spent about 2 hrs this evening on the footjoint of the flute. This is going to turn out to be a very fiddly job
I selected 19.0mm pads (from MusicMedic). This was not a straight-forward choice. 19.5mm pads fit, but needed to be pressed in a little and were a little tough to pull back out. 19.0mm pads drop right in and out, wrinkle less when fastened in, but are a little bit of a sloppy fit. I may decide to switch to 19.5mm. I don't like the way the 19.0's don't quite center themselves.
I am using 18mm shims in .004", and also have .001" available. I liked the way the 18mm shims fit with 18.5mm pads, but they are a little small for 19-19.5mm pads. Also, with 2.7mm thick pads on this armstrong, some keys are requiring up to 6 .004" shims. I may decide to order some larger and thicker shims, maybe .008" or even thicker, and 19.0mm.
Before I started, I mapped out the tone hole levels. The D key is the worst, low by about .002" north-south (along the axis of the flute). I'm not ready to tackle tonehole leveling, so I intend to handle this with partial shims. I did actually get the pad to touch east-west (front and back), but I haven't applied the partial shims yet.
At first, I put the pads into each cup in a random orientation, put the keys on the flute, and located high/low spots with a .001 feeler strip. I added shims to get coverage correct front to back. I then found high spots at odd angles. At first I tried partial shims, and on my first try I didn't get the mirror image correct. Then I started using my microscope slide - I drew a diagram of the pad coverage on the glass slide and then flipped it over (genius! - at least for a beginner). Then I had a little bit of a revelation: I was seeing errors of nearly .010", much more than the tone holes, not sure about the key flatness or levelness. I am assuming the largest error is really thick parts of the pads themselves. Instead of shimming the wierd angles, I rotated the pads until the high spots were at the front of the keys. Then I removed shims to get them level front to back. It worked relatively well.
Tomorrow I'll pick up where I left off and see if I can get the D to cover. The C# and C are pretty good right the way they are. I need to regulate them. Right now the roller isn't quite closing the C key.
I haven't done anything yet to try to get the wrinkles out of the pads. I have read about "steam ironing" them with a hot slick, and also about just dampening and letting them air dry. I may be about ready to try these approaches.
Then I have to figure out how to "seat" the pads. The Burkart-Phelan book recommends dampening the pads (although it actually says shims which doesn't make sense to me), heating the key cups, and using moderate finger pressure to hold the keys closed while the pads dry. It doesn't say how long and doesn't talk about clamps.
Sorry about the length. If the resident techs are still reading, I'll graciously accept suggestions and comments.
Thanks,
Jim
|
|
 |
|
Re: Armstrong 104 Repad
08:25 on Saturday, March 6, 2010
|
|
 |
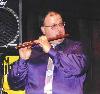 JButky (657 points)
|
I haven't done anything yet to try to get the wrinkles out of the pads. I have read about "steam ironing" them with a hot slick, and also about just dampening and letting them air dry. I may be about ready to try these approaches. |
|
Some techs do iron pads. I just wet them and blot them with a paper towel. The important part is to get rid of the wrinkles. If your pad exposure is too great for the pad nut height you will introduce more wrinkles than necessary and create an effect of hardening the felt a little making the pad much more difficult to seat with shims. You find this sometimes on flutes where the keycup angles where not setup properly from the design aspect.
Then I have to figure out how to "seat" the pads. The Burkart-Phelan book recommends dampening the pads (although it actually says shims which doesn't make sense to me), heating the key cups, and using moderate finger pressure to hold the keys closed while the pads dry. It doesn't say how long and doesn't talk about clamps. |
|
Seating and leveling are interchangeable words. It is the process of doing what you are currently doing: adjusting pads to cover or "seat" on the tone hole
The last step is putting a final impression in the pad. This is dependent on the type of felt and how well your seating job and/ or tone hole condition.
The more level the tone hole and/or better the seating job, the less impression you will need. There is as much art to figuring out this as anything else. Water heating and long clamping time yields maximum m deep impressions. If you've done a fantastic job of tone hole prep/pad seating, the final step can be almost eliminated.
If you've done a great seating job, Start with some clamping pressure and dry heat. A leak light in the body of the flute is usually more than sufficient. As soon as the flute gets hot turn it off and then remove the clamps when the body is cool. Should take about 5 minutes.
You can lightly dampen the pads. I'll use a wet paper towel (squeezed out). Fold an edge over to slip between the pad and the tone hole and give it a press to slightly dampen a pad. Adjusted flute key clamps then usually keep the keys shut while the leak light does it's job. If you don't have clamps, many techs use a ribbon and wrap the ribbon around to keep the key closed.
You'll be able to figure out over time, the correct amount of time, heat/no heat, damp/no damp, clamping pressure, to get it right.
For example: some wet and clamp without any heat. It's part of the learning curve...
Try those and see what works easiest for you.
Joe B
|
|
 |
|
Re: Armstrong 104 Repad
20:53 on Saturday, March 6, 2010
|
|
 |
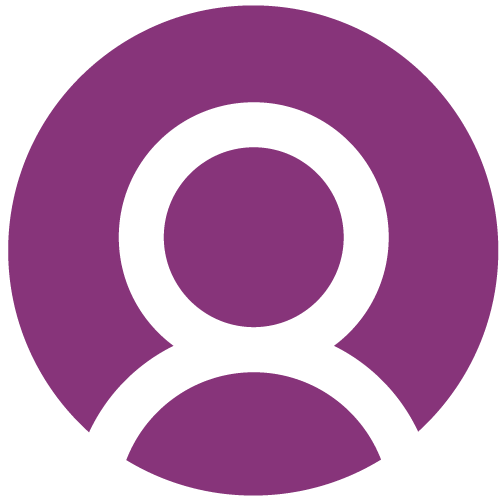 jim22 (247 points)
|
I finally got the D# key to cover - it took hours. I'm still not sure why it finally caved. After that I decided I needed to address the wrinkles in the footjoint pads. I tried dampening and let them air dry, which worked somewhat. Then I tried dampening and smoothing with a hot pad slick. That seemed to work really well.
Without any attempt to "put an impression" on the pads, the flute actually plays. I think I have some leaks in the body because I've been fiddling with it's pads and adjustments, but the footjoint pads seem to seal reasonably well. I'll call that a success.
I moved on to the body. Took off all key assemblies and changed the pad in the G key (LH pinky, I may be getting my key names mixed up). I popped in the prescribed shims and a fresh pad. This time I dampened and ironed with the hot pad slick before even reinstalling. I couldn't believe it, it covered perfectly on the first try! Next I did the thumb (B?) key. Same process, same results - perfect on the first try! I began to get (over) confident. :0
Next I tackled the offset G keys. They appeared to be straight, so I popped in the shims and pads, dampened, ironed, and put them on the flute. One covered perfectly. The other seemed to be universally high. I removed the pad and installed .002 of shims. Maybe to the wrong key, not sure, I may have gotten myself turned around. From that point on things got confusing. I found one key hitting in back. I moved the shims to the "other" key. No luck. I removed half of a .004 shim. Then I had leaks on both pads at odd angles. Another couple hours later I put it aside for tonight.
I'm starting to wonder about the repeatability of fastening the pad into the key cup. I did mark the pads to keep them in the same orientation in the key cups. It's all good experience I suppose. I'll have another go at it tomorrow.
Jim
|
|
 |
|
Re: Armstrong 104 Repad
21:07 on Sunday, March 7, 2010
|
|
|
Re: Armstrong 104 Repad
22:43 on Thursday, March 11, 2010
|
|
 |
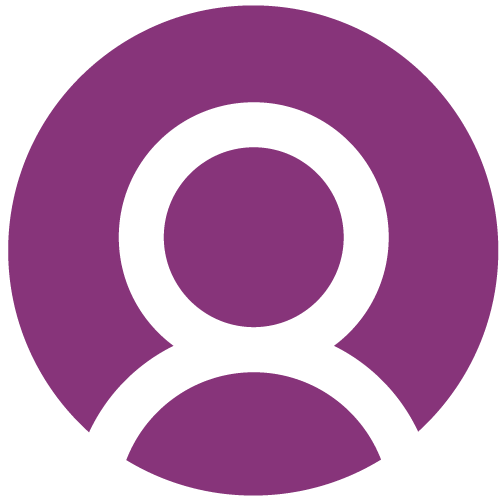 jim22 (247 points)
|
Tonight I finished seating the RH pads, none of which went particularly easily. First thing I did was to rotate the pads to get the thick parts at the back - I started with shims installed. One needed part of a shim removed, but the others all needed additional partial shims.
I haven't changed the three small pads yet. They are still on back-order, but I had not yet removed the original ones. I put the flute back together, and had to adjust the Bb cork to the new pad height. After some fiddling with the cork height and the adjusting screws THE FLUTE PLAYED!
I have not yet even tried to get tone hole impressions on the pads. I'll probably have a go at that next. I hope I don't screw up the shimming too much. The other thing to address is venting and lost motion. Then I really need to find a nicer headjoint for it (I bet that would be tough).
When I do the second flute, I think I'm going to try to get screws and washers to attach the pads to replace the plastic caps. It took me lots of on/off cycles to get the shims right.
Important lesson learned: Be very careful recording the high and low spots on the pads, and be extremely careful to flip those diagrams over before putting the shims in. If you put the shims in the wrong place because you forgot to flip the diagram, things get really weird really fast  I've been drawing on a glass microscope slide. When I take the keys off and flip them over, I flip the glass slide over.
Before I do the next flute, I'm going to order more shims, including .002" and .008" or .012", and probably some 19mm ones for the foot joint pads.
I better not quit my day job - I've got probably 12 hours into the project so far. The good news is I'm gaining confidence. Eventually I'd like to work on my DeFord - maybe. I don't think I'd do any permanent damage, anyway.
Jim
|
|
 |
|
Re: Armstrong 104 Repad
21:08 on Sunday, March 14, 2010
|
|
|
Re: Armstrong 104 Repad
20:41 on Thursday, March 18, 2010
|
|
 |
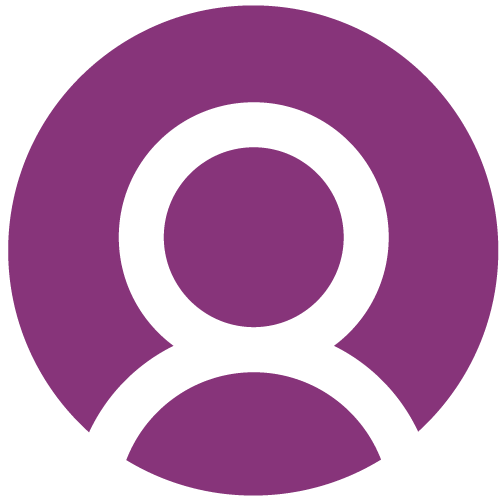 jim22 (247 points)
|
I didn't make up the part about loosening up the pads, it's in the Burkart-Phelan book, but next time I'm trying it without to see if I can get more pads that are "just right" with no partial shimming.
Other than that, I made a little progress tonight.
First I took a look at the venting on the trill and C# keys. They were vented significantly less than .100", so I sanded the corks to bring them closer.
Then I fiddled with some of the regulating adjustments. I ended up deciding the D key was not sealing well and I decided to try to put bit of a tonehole impression on it. I closed the key on a wet paper towel for 30 seconds, then held the key closed and heated the area with a hair dryer. I figured it was hot enough when my fingers started to burn.  Then I turned off the heat and blew cold air until the area cooled off. That left reasonably nice impressions and made the high and low areas pretty obvious. I did this on the lowest two keys on the body. When I was done, the flute played pretty well. I can see the value in a set of clamps. They would allow a controlled amount of pressure and save my burning fingers.
Still need to address lost motion, and maybe improve the coverage on a few more pads. Not ready to hand to a young player yet, still requires too much finger pressure. It might be my imagination, but I think the tone is less stuffy. I'm wondering if the venting helped that a little.
Jim
|
|
 |
|
Re: Armstrong 104 Repad
20:58 on Thursday, March 18, 2010
|
|
|
Re: Armstrong 104 Repad
08:32 on Saturday, March 20, 2010
|
|
|
Re: Armstrong 104 Repad
17:46 on Saturday, March 20, 2010
|
|
 |
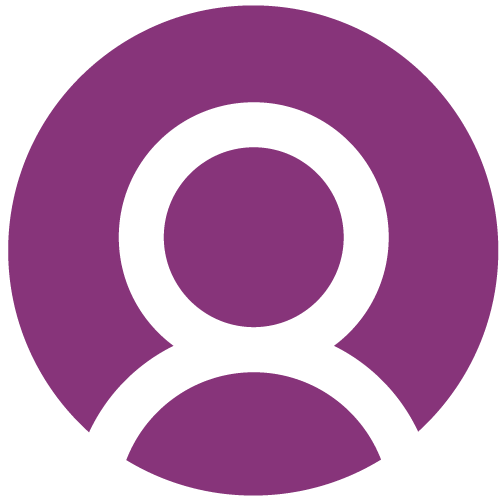 jim22 (247 points)
|
"Most people starting on flute adjustment have no idea how lightly they must press a key while doing that feeler detection, in order to get good results."
Uh, Oh.... back on my head
Are you sticking with the idea that only full shims should be used? If one levels the toneholes, that would eliminate the need for shims to compensate for them. I guess we can assume the key cups are flat, or maybe flatten them or use pad stabilizers. Then the plane of the tonehole rim and the plane of the key cup/stabilizer can be aligned by shimming with full shims for height and by bending keys for left right. But are the pads really of uniform thickness all the way around - down to less than .001"?
I think I have more work to do. Thank you for your insight. Please don't take any of this as argumentative - it's not meant to be. I'm just amazed at the level of effort this is taking so far.
Jim
|
|
 |
|
Re: Armstrong 104 Repad
19:09 on Sunday, March 28, 2010
|
|
 |
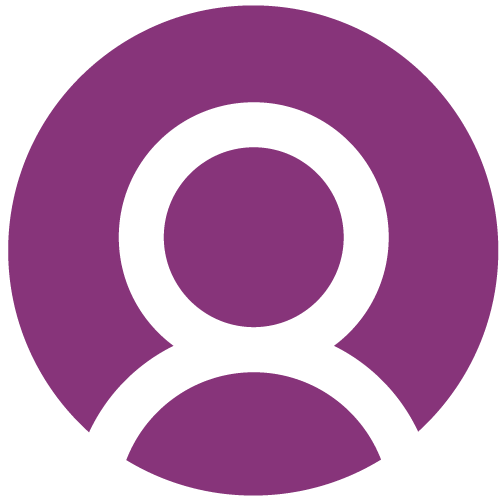 jim22 (247 points)
|
"Finished" the padding this afternoon. I ended up making one more pass across each pad, reshiming where I found issues. The very last pad I looked at (RH3, D# I think) was a mess. The tonehole was a little un-flat, but it was very un-level. That would have been a good spot to bend the key to align with it, but that's still quite beyond my skill level. As I finished with each pad, I dampened it, held it closed with finger pressure, and heated with a hair-dryer. The result was moderate tonehole impressions on each pad.
This time, the keys went into regulation on the first try. I played it for a half-hour or so, and it seems to seal well right now. I'll get it out every few weeks for a while and see how it holds up.
I do still need to work on the springs and venting. I've got one spring that's loose and I haven't figured out what to do with that yet.
So what did I learn?
1. Selecting pads requires having a moderate collection on hand - reasonable for a professional, but represents an investment for an amateur that does a flute now and again. Ditto for having a collection of shims on hand.
2. There are other critical skills and tools that the professionals have that an amateur is unlikely to have, e.g, mandrel, tone hole leveling and key bending tools, as well as the skills to use them.
3. Shimming seems to be a nightmare, especially lacking the ability to make the toneholes nearly perfect and bend the keys to fit them. I do think there is a middle-ground between perfectly aligned, flattened and shimmed and "close enough that a tonehole impression will make up the difference". I'm not exactly sure where it is. This flute, for example, had been professionally repadded about 2 years ago. There were single .005" partial shims under 3 of the pads, but otherwise the pads were simply bolted in. I did eventually have to shim several of those pads myself because they became light in front and did not seal. We'll see if my pads hold up any better. The next tech who works on this flute is going to think the work I did was hilarious. It took me probably 20-30 hours, but I think I could to the next one in a little less.
So, will I try again with the second Armstrong? Maybe. I need to research replacing the plastic snaps with screws and washers, or I wouldn't even try it. I probably had some pads off dozens of times.
Will I use MusicMedic pads again? Maybe. I came across one with a defect that made it unuseable, and I needed to smooth the backs of two or three of them, but they seemed mostly ok as far as being flat. I might try JLSmith pads just for the experience. MusicMedic is awesome about shipping small quantities of diverse products like I needed, including free shipping and shipping materials.
Will I work on my DeFord? Probably not. I think it would really benefit from some professional attention. If it had one or two split pads, I might try them myself, but it needs a real overhaul and I think it would be worth paying someone to do it.
I am considering bidding on a VERY tired piccolo which I would have to fix up
Thank you all for your support. I hope my experiences are useful to others.
Jim
|
|
 |
|
|
|
|