Buffet E- 11, R-13 question
Buffet E- 11, R-13 question
14:56 on Saturday, February 6, 2010
|
|
|
Re: Buffet E- 11, R-13 question
03:50 on Sunday, February 7, 2010
|
|
|
Re: Buffet E- 11, R-13 question
08:10 on Sunday, February 7, 2010
|
|
|
Re: Buffet E- 11, R-13 question
08:21 on Sunday, February 7, 2010
|
|
|
Re: Buffet E- 11, R-13 question
13:54 on Sunday, February 7, 2010
|
|
|
Re: Buffet E- 11, R-13 question
16:01 on Sunday, February 7, 2010
|
|
 |
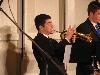 krosskuntryrunne r
|
Posted by krosskuntryrunner
Are you sure the clarinet is made of rose wood?
I have never heard of an R-13 or any buffet being rose-wood
|
|
 |
|
Re: Buffet E- 11, R-13 question
07:13 on Tuesday, February 9, 2010
|
|
 |
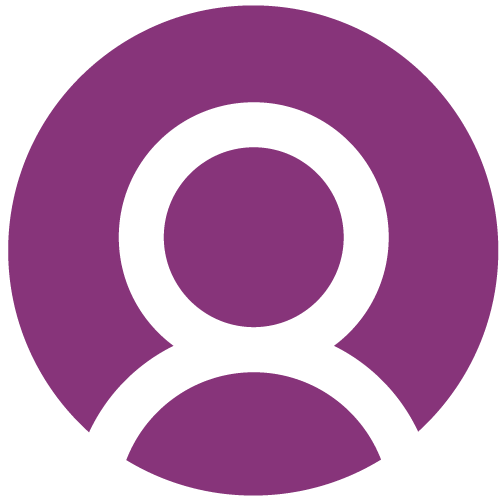 Koopyetz (15 points)
|
Hello Rosewood is what was mentioned by current R-13 owner.
I did a search regarding the use of Rosewood for clarinets. I have pasted what I found from my search.
Ask clarinetists why Grenadilla wood was chosen for clarinet making and ninty-nine out of a hundred (perhaps more) would say, "Because of the sound."
They would, in point of fact, be wrong. The sound was not why Grenadilla was chosen––and it was not clarinetists but clarinet makers who made the choice.
That may sound absurd to the many end users who believe uncritically that manufacturing decisions are made according to the criteria they themselves regard as important. Those of us who have been in manufacturing know better. We know that manufacturers often make products a particular way, with certain materials, not because it then gives the best result for the end-user, but because doing so gives them fewer manufacturing problems.
Clarinet manufacturing is no exception to this upspoken but widely practiced manufacturing rule. The fact is there are many other woods that have better musical qualities than Grenadilla wood; woods that have a better, more stable tone; woods that have a better response. Honduran Rosewood immediately comes to mind in this regard, but there are others. It produces a darker, more coloristically stable tone of greater beauty than Grenadilla and the response is quite superior throughout the dynamic and pitch range of the clarinet.
So why was it not used rather than Grenadilla?
Very simple: making Honduran Rosewood clarinets is a manufacturing nightmare. First, it does not machine nearly as well as Grenadilla. There is much more waste involved in processing it, and waste is lost money and time. The tone holes of the natural wood are so pitted that pads leak terribly. In order to provide a leak proof surface for Rosewood clarinet requires tone hole inserts. Rosewood cracks more frequently than does Grenadilla. Finally, because the wood is so porous, it absorbs great amounts of moisture, causing bore dimensions of the barrel and upper joint to be very unstable. Such instability causes tuning to go "wacko" and the clarinet can feel "blown out" after only a short time of playing. The only solution is to line a large amount of the upper joint bore in hard rubber to stabilize dimensions and reduce cracking. Honduran Rosewood barrels are also usually lined in hard rubber for the same reasons.
Each one of these problems is frustrating to manufacturers, each is difficult, time consuming and costly to solve, and any one of them would label Honduran Rosewood as unviable for large scale production from the manufacturer's point of view––but not from the player's!
In the end, Grenadilla was chosen above other woods because of practical concerns: it was comparitively stable, machined like metal, did not crack as often as other woods and generated less waste in the manufacturing process (this saved money).
Because of these qualities, Grenadilla wood made it possible for manufacturers to economically produce wood clarinets on a large scale.
There is no doubt these features inherent in Grenadilla wood are practical concerns for clarinetists as well as manufacturers. No one wants a clarinet that cracks, leaks or is dimensionally unstable. But as important and practical as these issues are, none has anything to do with the artistic concerns of the clarinetist; beauty of tone, responsiveness and stability of tone in dynamic changes, etc.
|
|
 |
|
|
|
|